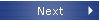 |
Page 2 |
Newsletter 121, Summer 2018 © Hampshire Mills
Group |
From Needles to Putty, Forging to Flour
A talk by Peter Hill to the HMG meeting on 24 March 2018
Putty
Alison Stott (with minor additions by Dave Plunkett)
Photos by Peter Hill
and Dave Plunkett
, Forging to
|
Peter started by saying that
TIMS (The International Molinological Society) hold
a symposium every four years in a different country
when mills of the area are visited and learned
papers given; between these symposiums a mid-term
excursion is held, again in a different country, but
in this case just the mills are visited and there
are no lectures. In 2017 this took place in the
Midlands of England when a total of 30 mills were
visited during the week. His
talk took us on a lightning tour of 17 watermills
and 5 windmills. A selection are mentioned below.
|
Thwaite Mill,
near Leeds, last produced linseed oil putty. It has
two internal waterwheels driving edge runner stones
to crush chalk; this was then mixed with water and
the resulting slurry evaporated, using hot air from
furnaces to produce whiting. It was mixed with
linseed oil from Canada to produce putty for
timber-framed windows, with a rubber compound added
if it was to be used for metal frames.
|
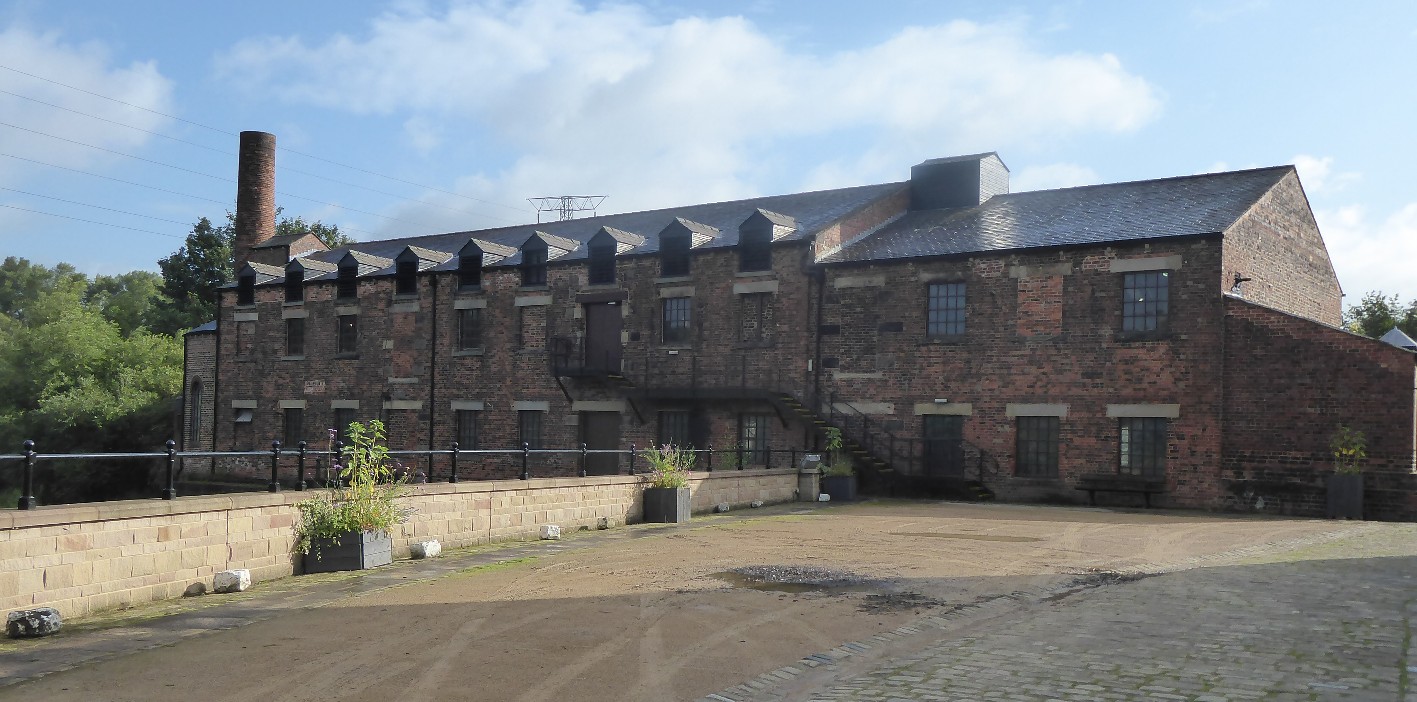 |
Redditch Needle Mill
demonstrated a very laborious and complicated
process. Briefly, pre-heated wires were drawn out
to the required thickness, cut into lengths, and
straightened by heating and rolling; at this point
they became known as ‘stiffs’. The most perilous
part of the process now took place. An operator put
100 ‘stiffs’ between the palms of his hands and held
them against a fast revolving stone until sharpened.
Slivers of steel might become embedded in his eye
and metal and stone dust filled the air; life
expectancy was 28 to 35 years. A further process to
harden and glaze the needles took place before final
packaging and distribution around the world.
|
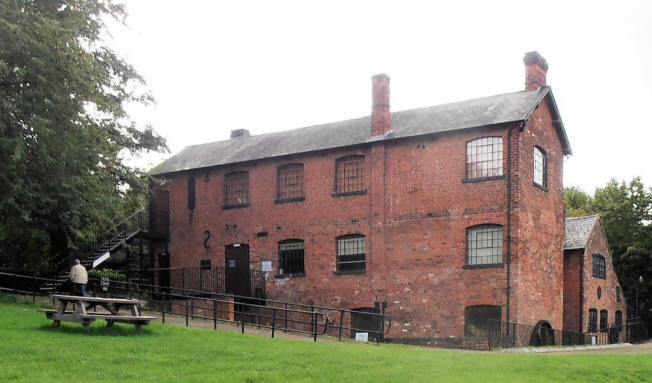 |
Shirley’s Bone &
Flint Mill,
Etruria, was powered – unusually – by a beam
engine. Flint and bone (previously boiled) were
calcined in kilns at high temperature, transferred
to grinding pans, mixed with water, and tumbled
round the pans by one-ton chert blocks until in
suspension. This was run off to settle in ‘arks’ on
the floor below when, finally, the resultant ‘slop’
was barrelled up and sent off to customers to make
bone china crockery.
|
Shepherd Wheel
Grinding Mill,
Sheffield. Edging, sharpening, and polishing of
tools took place here with no less than 18
grindstones of various dimensions being driven from
line shafting. The grinder sat astride wooden
horsing and from the age of 9 his son could become
an apprentice, sitting behind him. It was a
hazardous job, the air was filled with sandstone and
metal dust; life expectancy was 35 to 40 years.
|
On this trip Peter
also visited several corn mills. One with an
unusual bit of history was New Hall Mill, Sutton
Coldfield, where, in 1899, on a single day flour was
ground and a loaf of bread baked and sent to Queen
Victoria for her golden jubilee – and the same was
done for Queen Elizabeth’s silver and golden
jubilees.
|
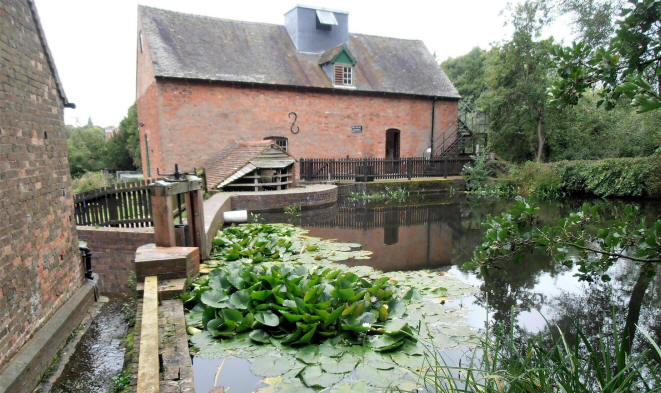 |
Ashford Bone &
Bobbin Mill (where access to the inside was not
possible) had originally been a saw and wood-turning
mill which made bobbins for the textile industry
before eventually making self-assembly carts and
wheelbarrows. The bone crushing mill was not for
the pottery industry but for producing bone-meal
fertiliser.
|
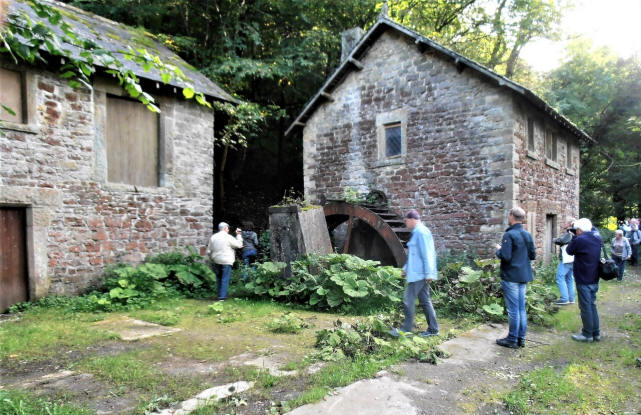 |
His final two
water-powered mills were two huge commercial mills.
Belper North
Cotton Mill
was built in 1803 using cast iron beams and supports
following a fire which destroyed the previous mill.
This enormous and impressive building now stands
more or less empty
next to the equally
impressive partner, the East Mill. On the same site
adjacent is the Belper Hydro Electric Station,
restored and feeding power into the grid.
Quarry Bank Cotton Mill,
Styal, of 1784 expanded over many years with
additional waterwheels and then two turbines to
drive the cotton spinning machinery – this is a very
well-known mill and is probably familiar to most
members. Demonstrations of the early methods of
spinning and weaving are provided daily.
Peter
also showed slides of five windmills visited on this
tour, all corn mills, ranging from the post mill
from Danzey Green (below left) at the
Avoncroft Museum, to the six-sailed stone tower mill
at Heage, Derbyshire,
which is in full working order.
His
final slide was an amazing view of Chesterton
Windmill, Warwickshire, (below right) caught by a
shaft of light from the setting sun.
The
members present thanked Peter for once again coming
to talk to HMG and for interesting and entertaining
us so well.
|
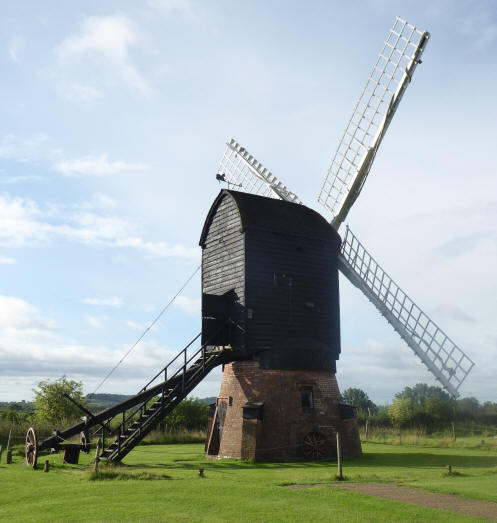 |
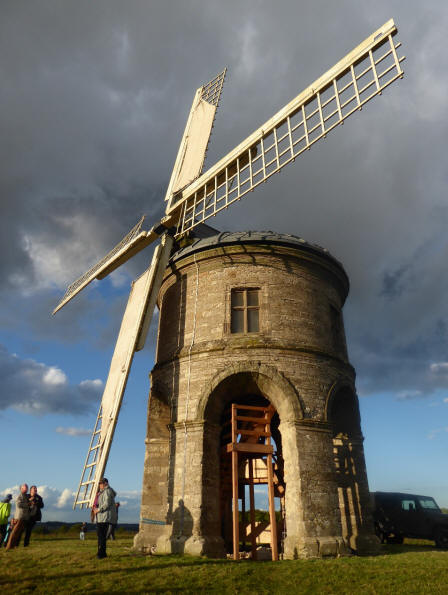 |
Daniels Mill
near
Bridgnorth
Editor:
Peter included this restored corn mill in his
talk, although it is not mentioned in Alison’s
report. I have added it here as it shows the
backshot suspension wheel with its unusual water
supply.
|
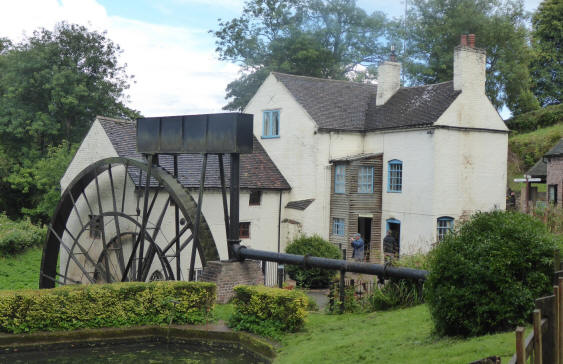 |
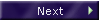
|
|